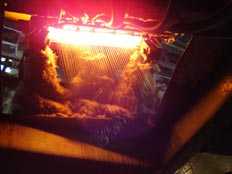
Технологии производства базальтовых волокон, особенно непрерывных волокон, достаточно новы, имеют ряд принципиальных особенностей, связанных с исходным сырьем – базальтами.
Базальтовые породы (базальты, андезитобазальты, базаниты, диабазы, габро, долериты, амфиболиты, андезитовые порфириты и другие породы) относятся к основным породам магматического происхождения, имеют высокую природную химическую и термическую стойкость. Базальтовые породы – однокомпонентное сырье обогащение, плавление и гомогенизация которых произведены в результате древней вулканической деятельности. Особенностями базальтов является то, что основные энергозатраты по их подготовке к производству волокон выполнены природой.
Для каждого типа базальтов необходимы свои особые технологические режимы и параметры производства волокон.
Основные технологические процессы
При всем многообразии таких технологических режимов можно выделить основные технологические процессы:
- плавление базальтов, переход базальтов при плавлении из кристаллического состояния в аморфное;
- гомогенизация расплава по химическому составу и степени аморфности;
- подготовка расплава к выработке для достижения однородности расплава и необходимых параметров по вязкости и выработочным характеристикам;
- выработка расплава через фильерный питатель;
- вытяжка непрерывных волокон.
Процессы плавления, гомогенизации и подготовки расплава проходят при высоких температурах 1400 – 1600 °С и связаны с определенными энергозатратами. Далее технологии переработки базальтовых волокон в материалы и изделия не связаны с высокотемпературными процессами и производятся с применением «холодных технологий». Поэтому технологии производства БВ являются по сути энергосберегающими и экологически чистыми.
Непрерывное базальтовое волокно
Технологии производства непрерывного базальтового волокна (НБВ) при всей своей внешней кажущейся простоте представляют собой довольно сложные процессы. Ранее широкое применение НБВ сдерживалось сложностью промышленного оборудования и технологиями их производства. Себестоимость производства НБВ была относительно высока и существенно превышала стоимость стекловолокна.
Технологии производства базальтовых волокон при всем внешнем подобии значительно отличаются от производства стеклянных волокон, что связано с рядом факторов:
- химический состав базальтов существенно отличается от стекла;
- расплавы базальтов непрозрачны для теплового излучения;
- базальты – это уже готовое природное сырье, гомогенизированное по химическому составу;
- в процессе плавления базальтов нет операций, присущих при варке стекла, осветления, остужения и др.
Эти особенности базальтов определяют специфику технологии производства и соответственно технологического оборудования для производства НБВ.
Cебестоимость производства
Разработки последних лет специалистов компании в области технологий и оборудования производства НБВ позволили значительно снизить себестоимость их производства.
В Китае достаточно высокие цены на энергоносители (природный газ и электроэнергию), даже по сравнению с Западной Европой. Поэтому специалисты компании провели ряд разработок, позволивших в два раза снизить расход газа и электроэнергии на производство единицы продукции. Естественно, что эти разработки специалистов компании защищены патентами на технологии и оборудование.
Технологии и оборудование производства НБВ достаточно новы и имеют большие резервы своего развития. В настоящее время компания проводит ряд работ по исследованию процессов плавления базальтовых пород, исследованию выработочных свойств расплавов базальтов.
Цель проведения исследований – совершенствование технологий, снижение энергопотребления, повышение производительности процессов производства НБВ (см. статьи «Исследование процессов плавления базальтов», «Исследование выработочных свойств расплавов базальтов при производстве НБВ»).
Базальтовое супертонкое волокно
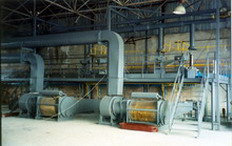
Технологии производства БСТВ достаточно отработаны в течение более 30 лет их промышленного применения и хорошо себя зарекомендовали в промышленности.
Кратко традиционная технология производства БСТВ состоит из следующих процессов:
- загрузка базальтовой измельченной породы в печь;
- плавление базальта и гомогенизация расплава в печи;
- выработка расплава базальта из фидера печи через фильерный питатель в виде первичных волокон; раздув первичных волокон горелкой раздува в штапельные супертонкие волокна;
- формирование холста БСТВ на приемном конвейере.
В технологическом процессе производства БСТВ имеются два относительно энергоемких процесса – плавление базальта и раздув первичных волокон высокотемпературным потоком.
Последние разработки специалистов компании позволили усовершенствовать технологический процесс производства БСТВ, разработать установки нового поколения BSTF с низким энергопотреблением – BSTF 20 и BSTF 40.
Базальтовая чешуя
Кратко технология производства базальтовой чешуи (БЧ) состоит из следующих процессов:
- загрузка измельченной базальтовой породы в камнеплавильную печь;
- плавление и получение расплава базальта в плавильной печи;
- выработка расплава через фидер печи и фильерный питатель;
- получение чешуи на формующем устройстве;
- сепарирование фракций базальтовой чешуи;
- дозирование и упаковка БЧ.
Данная технология позволяет при относительно низких энергозатратах производить ценный материал для покрытий, производства композиционных материалов – БЧ.
Представляют интерес технологии применения БЧ для производства износостойких, химическистойких защитных покрытий и композиционных материалов – методом напыления, обеспечивающие высокую производительность и качество.
Технологии энергосбережения
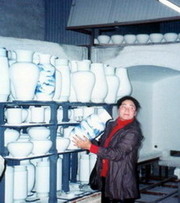
Технологии энергосбережения в промышленности всегда представляли интерес. Так как в промышленности расходуется до 80 % потребляемых энергоресурсов.
Опыт работы в этой области показывает, что применение технологий энергосбережения при проведении реконструкций действующих и строительстве новых печей и термического оборудования позволяет снизить энергопотребление от 20 до 50%.
Особую актуальность технологии энергосбережения приобретают в последнее время на фоне роста стоимости энергоносителей – газа, нефти, электроэнергии.
в Китае стоимость энергоносителей достаточно высокая, поэтому применение технологий энергосбережения представляет большую выгоду.
Справка. Cтоимость 1000 м³ природного газа (NG) в Украине составляет $ 72– 75 , в России – $25 – 47, в Китае – $130 – 320. Соответственно сроки окупаемости мероприятий по энергосбережению в Китае будут более короткими.
Технологии энергосбережения, включают применение современных, высокоэффективных материалов, оснащение газогорелочного тракта печи системами рекуперации тепла и регулирования, автоматизацию контроля и управления технологическими процессами и ряд других инженерных решений. Это позволяет добиться снижения потребления энергоресуров до 40%, а при реконструкции старых печей этот показатель становится ещё выше.
К настоящему времени накоплен большой опыт применения волокнистых материалов при реконструкции и строительстве многих типов промышленных печей на Украине, России, Белорусии.
Практическая эксплуатация таких печей подтверждает высокую эффективность и надежность применения волокнистых материалов и экономичных систем отопления.
Компания только начинает эти работы в Китае. Но результаты работ по реконструкции камерной печи обжига фарфора в Jingdedzhen при низких вложениях денежных средств уже позволили снизить потребление LPG на 25% (Информация о реконструкции печи обжига фарфора ).
Высокотемпературные композиционные материалы
Компанией разработаны весьма перспективные технологии производства высокотемпературных материалов и изделий с применением безобжиговых, «холодных» технологий. Суть этих технологий заключается в создании высокотемпературных материалов по «холодным» технологиям, без применения традиционной при производстве огнеупорных материалов операции обжига.
При этом предлагаемые высокотемпературные композиционные материалы (ВТКМ) обладают новыми характеристиками:
- низкой удельной плотностью от 300 до 1200 кг/м³;
- обладают теплоизоляционными свойствами;
- не боятся резких перепадов температур;
- легко формуются и поддаются механической обработке при изготовлении изделий сложной конфигурации.
Опыт применения высокотемпературных композиционных материалов, в том числе и в Китае, показал их высокие характеристики и эксплуатационные свойства при производстве футеровочных работ и ремонте печей, при изготовлении горелочных камней газовых горелок и горелок LPG и, особенно, при футеровке фильерных питателей для производства базальтовых и стеклянных волокон.