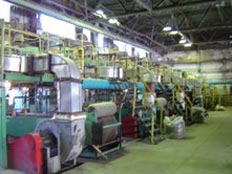
Basalt Continuous Fibers (BCF) Production Techniques
Production techniques of basalt fibers, especially (continues basalt fibers) are new enough and have a number of the basic features connected with initial raw material – basalts.
1/3 of the Earth's crust consists of basalts. Basalts had lain many millions years on a surface of the Earth. Basalt breeds (basalts, andesito-basalts, diabases, gabbro, andesito-porphyryte and other breeds) concern to the breeds of a magmatic origin. Basalt breeds are one of the strongest natural silicate breeds. Basalt breeds – unicomponent raw material. Primary fusion, enrichment and homogenization of basalt breeds were made by the nature, as a result of ancient volcanic activity. Safe and abundant, basalt rock has long been known for its thermal properties, strength and durability. Cost of extraction of basalt raw material is very low. Features of basalts are that the basic power inputs on their preparation for BCF manufacture are executed by nature. The special technological modes and parameters of BF manufacture are necessary for each type of basalts.
Basic technological processes
At all variety of such technological modes it is possible to allocate the basic technological processes:
- Fusion of basalts, transition of basalts at fusion from a crystal condition in amorphous;
- Homogenization of a melting basalt on a chemical compound and a degree of amorphy;
- Preparation of a melting basalt for achievement of uniformity and necessary parameters on viscosity and to workability characteristics ;
- Development of melting basalt through a bushing;
- Pull of continuous fibers.
Processes of fusion, homogenization and preparation of melting basalt pass at heats 1400 - 1600°C and are connected with the power inputs. An opportunity of producing of materials and products on the basis of BCF are not connected with high-temperature processes and made with application of various technologies such as forming, windings, pultrusion, spraying up and others «cold technologies». As a matter of fact Therefore BF Production techniques are energy saving and ecologically pure technologies.
Basalt Continuous Fibers (BCF)
Production techniques of basalt continues fibers (BCF) at all external seeming simplicity represent complex enough processes. Earlier wide application BCF restrained complexity of the industrial equipment and technologies of their manufacture. The cost price of BCF manufacture was rather high and essentially exceeded cost of fiber glass.
Production techniques of basalt fibers considerably differ from manufacture of glass fibers. It is connected with a number of factors:
- The chemical compound of basalts essentially differs from glass;
- Melting basalts are opaque for thermal radiation;
- Basalts are an available natural raw material and are homogenized on a chemical compound;
- During fusion of basalts there are no the operations inherent at glass fibers manufacturing, clarification, cooling, etc.
These features of basalts define specificity of the BCF Production Techniques and the Process Equipment for BCF manufacture.
Cost price of manufacture
Development of last years experts of the company in the technologies and the equipment of manufacture CBF have allowed to lower the cost price of manufacture for BF considerably.
In China high enough prices for energy carriers (natural gas and the electric power), even in comparison with the Western Europe. Therefore experts of the company have leaded a number of the development which has allowed twice lowering the charge of gas and the electric power on manufacture of a unit of production. These developments of experts of the company are protected by patents for technologies and the equipment.
Technologies and the equipment of CBF manufacture are new enough and have greater reserves of the development. Now the company spends a number of works on research of fusion of basalt breeds processes, research workability melting basalts. The purpose of carrying out of researches - perfection of technologies, decrease power consumption, increase of productivity of processes of CBF manufacture (see articles " Research of processes of basalts fusion ", " Research workability melting basalts by manufacture CBF ").
Basalt Super Thin fiber
Production techniques of super thin basalt fiber are fulfilled enough within more than 30 years of their industrial application and well itself have recommended in the industry.
Briefly a traditional BSTF technology consists of following processes:
- Loading the basalt crushed breed in the furnace;
- Melting and homogenization of basalt in the furnace;
- Production melting basalt from a feeder of the furnace through bushing in the form of continuous primary fibers;
- Blowing primary fibers in super thin fibers by attenuating blast gas burner;
- Formation STBF felt by the conveyor.
STBF technology by a drawing of primary fibers and blowing by their high-temperature gas stream is approved enough in industrial production. The basic features of installation of new generation BSTF-20 is application of new development and completion of the checked up technical decisions.
Installations BSTF 20 and BSTF 40 is process equipment of a new generation. Installations are intended for STBF manufacture of felts with diameter of fibers in 1-3 microns. Installations of BSTF series provide significant decrease electric energy demand.
Basalt scales (BSc)
Briefly a traditional technology for Basalt scales (BSc) consists of following processes:
- Loading the basalt crushed breed in the melting furnace;
- Melting and homogenization of basalt in the melting furnace;
- Production melting basalt through a feeder of the furnace ;
- Reception of scales on the forming device;
- Separation of basalt scales;
- Batching and packing of basalt scales.
Given technology allows making at rather low power inputs a valuable material for coverings, manufactures of composite materials on Basalt Scales basis.
Basalt Scales Technologies are interested for manufacture protective wear proof, anticorrosive and chemically proof coverings, the reinforced composite materials by method of spraying up, providing high efficiency and quality.
Energy Saving Technologies
Energy Saving Technologies in the industry always were of interest. As in the industry about 80% consumed power resources are spent. The operational experience in these area shows, that application of Energy Saving Technologies at carrying out of reconstruction operating and construction of new furnaces and the thermal equipment allows to lower power consumption from 20% up to 50%. Energy Saving Technologies gets the special urgency under growth of energy cost - gas, oil, the electric power recently. In China cost of energy resources is high enough; therefore application of Energy Saving Technologies represents greater benefit.
The information. 1000 m3 of natural gas (NG) cost make $ 75 - 95 in Ukraine, in Russia - $25 - 47, in China - $130 – 320 and times of recovery of outlay of actions on Energy Saving Technologies will be shorter in China.
Energy Saving Technologies include application of modern, highly effective materials, recuperation systems heat and regulation for gas-jet path of the furnace equipment, automation of the control and operate of technological processes and other engineering decisions. It allows achieving decrease in Power consumption up to 40%, and at reconstruction of old furnaces this parameter becomes still above.
By present time wide experience of application of fibrous materials is saved up at reconstruction and construction of many types of industrial furnaces in Ukraine, Russia, and Belarus.
Practical operation of such furnaces confirms high efficiency and reliability of application of fibrous materials and economic systems of heating.
The company only begins these works in China. In Jingdedzhen results of works on reconstruction of the chamber furnace for baking of porcelain at low total investments volume have already allowed to lower LPG consumption on 25% (the Information on reconstruction of the furnace for baking of porcelain).
High-temperature composite materials
Our company develops perspective Production techniques of high-temperature materials and products with application "cold" technologies. The essence of these technologies consists in creation of high-temperature materials on "cold" technologies, without application traditional by manufacture of fire-resistant materials of operation of baking.
Thus offered high-temperature composite materials (HTCM) possess new characteristics:
- In low specific density from 300 up to 1200 kg/m3 ;
- Highly heat-insulation properties;
- Are not afraid of sharp differences of temperatures;
- Easily are formed and give in to machining at manufacturing products of a complex configuration.
Experience of application of high-temperature composite materials including in China, has shown their high characteristics and operational properties by fettle works and repair of furnaces, at manufacturing stones of the gas and liquid-fuel jets, and, especially, as a materials for fettle of bushing at basalt and glass fibers manufacture.